Five main conditions may result pump cavitation and potentially damage pump impeller, chamber and bearing. Understanding of factors causing and affecting these conditions is rather important as it assist in troubleshooting pump cavitation problem. They are :
- Vaporization
- Gas and/or non-condensable fluid entrainment
- Internal recirculation
- Flow turbulence
- The Vane Passing Syndrome
Pump fluid vaporizes when operating pressure drop below its vapor pressure at specific flowing temperature. A process engineer must always keep this in mind and always to ensure pump fluid will be vaporized at minimum operating pressure along fluid path from suction vessel/tank to pump chamber at worst flowing temperature. Net Positive Suction Head (NPSH) is a parameter used to measure possibility of cavitation. A process engineer must always ensure NPSH available must always higher than NPSHr.
NPSHa > NPSHr
Obviously in order to maintain above requirement, a process engineer may aim to INCREASE NPSHa and / or DECREASE NPSHr.
Increase NPSHa
Now we shall further look into the possibility of increasing NPSHa :
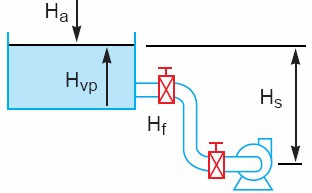
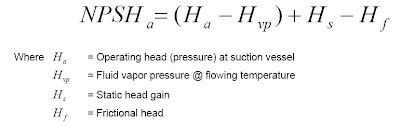
Process engineer should target to increase Suction static head & Operating head (pressure) and decrease fluid vapor pressure @ flowing temperature and frictional head.
As discussed earlier, there are few ways to increase NPSHa :
a) Increase suction line size to reduce friction head loss. Generally flow velocity is less than 1 m/s
b) Rearrange and /or redesign suction pipe work to minimise bends, valves and fittings
c) Raise suction vessel
d) Increase & maintain pressure in suction vessel
e) Reduce fluid vapor pressure i.e. subcool fluid In additional, process may pay consider the following :
f) Install a booster pump (if necessary)
g) Do not installed over-capacity pump (after suction line size is fixed)
h) Injecting a cooler fluid at the suction vessel (if practical) i) Insulate piping to avoid solar heating
j) Avoid recirculation line directly feed to pump suction line as pumping may raise fluid temperature
k) Use 45° elbows instead of 90° elbows to reduce friction
l) Do not select overly fine screens or intake filters and choose cleanable screen m) Avoid pocket at pump suction line
n) Ensure correct gasket installed at pump suction and tie flange to minimize air ingress
o) Use eccentric type reducer instead of concentric type
Sometime pump cavitation will only occur after the pump is operated for some period. Process engineer may look into the following factors :
- pipe liner has collapsed or solid / corroded material built-up and blocking suction strainer
- Tank vents blocked causing pressure dropped. Vent can be blocked frozen ice in cold weather, bird & insert, etc
- A bigger pump has been installed on existing system cause high line loss
- Install globe valve instead of gate valve at pump suction
- gasket protruding into the pipe
- Increased pump speed especially variable speed drive pump
Decrease NPSHr
AS discussed earlier, NPSHr is very much subject to design and construction of a pump and upto manufacturer. Nevertheless, Process engineer may advise to consider and include in the process design with the follow choices :
- Use a double suction pump where NPSHr can be reduced by almost 25%
- Use low speed pump
- Use pump with large impeller eye opening
- Install Inducer (inducers can cut NPSHr by almost 50%)
- Installer smaller pump by adopting 3 x 50% instead of 2 x 100%. Normally smaller pump may required lower NPSHr
Process engineer is advised to take some margin on the NPSH. The margin of 1 m is recommended for vaporization case.
Gas entrainment
Gas entrainment from suction vessel into pump fluid has an adverse effect on the pump impeller. Entrained gas will form bubbles in the flowing fluid and the bubbles will collapse as they pass from the eye of the pump to the higher pressure side of the impeller. Collapse of entrained gas as compare to bubble formed due to vaporization, it has lower impact to the pump impeller. The main effect is entrained gas is capacity loss.
There are number of ways may result gas entrained into pumping fluid :
- Through the packing stuffing box. This occurs in any packed pump that lifts liquid, pumps from a condenser, evaporator, or any piece of equipment that runs in vacuum
- Valves located above the water line
- Through leaking flanges
- Pulling air through a vortexing fluid
- If a bypass line has been installed too close to the suction, it will increase the temperature of the incoming fluid
- Any time the suction inlet pipe looses fluid. This can occur when the level gets too low, or there is a false reading on the gauge because the float is stuck on a corroded rod.
Internal recirculation
Internal recirculation occurs at leading edge of the impeller, close to the outside diameter, working its way back to the middle of the vane. Similar condition occurs at pump suction eye as well. Fluid recirculates will results its velocity increase and subsequent pressure drop until it vaporizes. Bubbles may collapse quickly at the surrounding higher pressure region within pump impeller.
Flow turbulence
Flow turbulence is always occurred of the pump suction with impeller impacting the incoming fluid. Change of incoming fluid will change velocity and it operating pressure and results short term cavitation.
The Vane Passing Syndrome
Vane passing syndrome and causing cavitation occurred when the OD of the impeller passes too close to the pump cutwater. The velocity of the liquid increases as it flows through this small passage, high velocity lowering the fluid pressure and causing local vaporization. The bubbles then collapse at the higher pressure region just beyond the cutwater. This phenomenon occurred at the center of the impeller vane.
JoeWong
No comments:
Post a Comment